Theta Technologies News
Issue 1
BAE Systems and AMRC North West put RD1-TT to the test
Could this brand-new non-destructive testing technology be key to the future development of metal additive manufacturing?
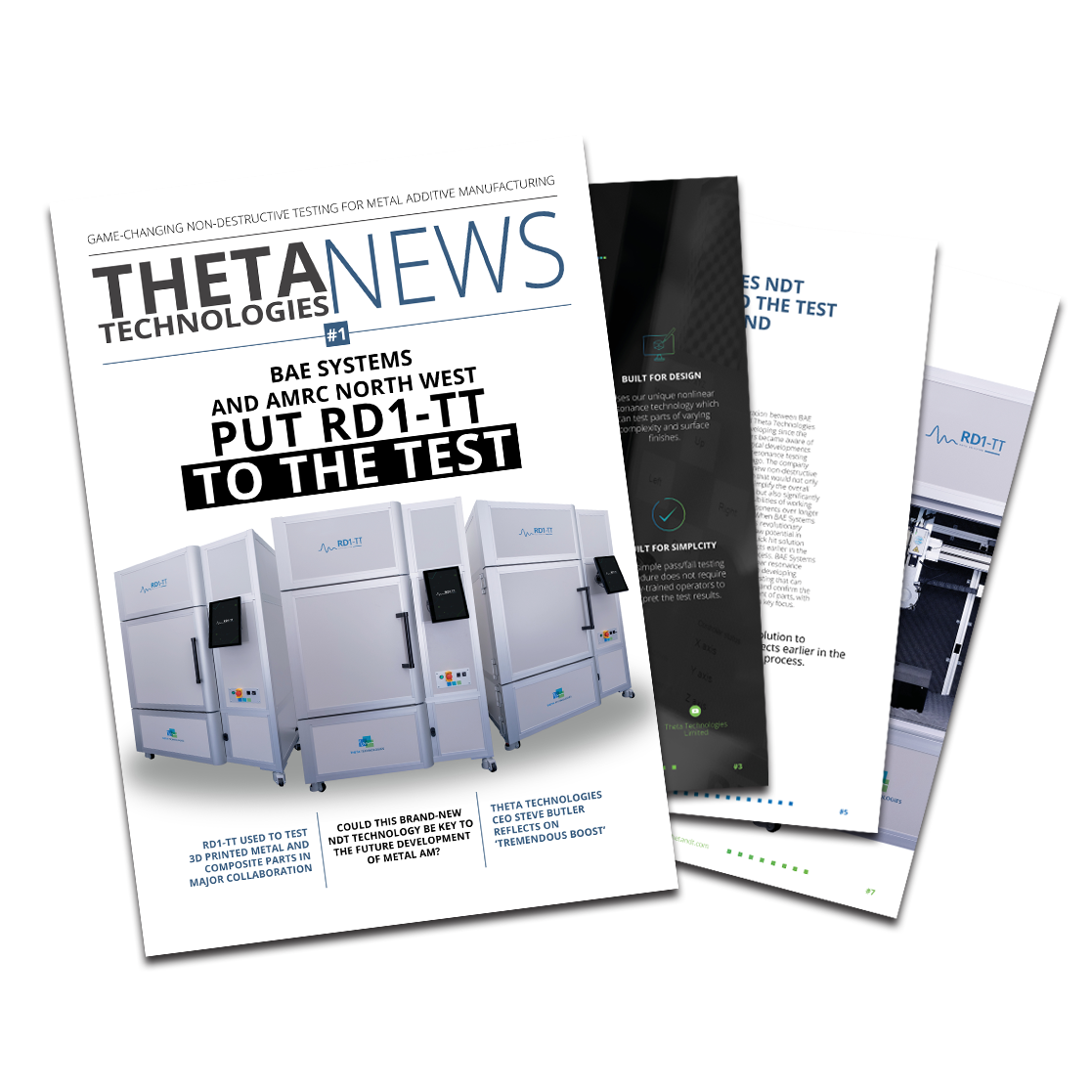
the full story
BAE Systems and AMRC North West put RD1-TT to the test
Theta Technologies are excited to announce a collaboration with major aerospace and defence manufacturers BAE systems, AMRC North West, part of the University of Sheffield Advanced Manufacturing Research Centre, and the High-Value Manufacturing Catapult. The collaboration will soon see Theta’s first commercially available non-destructive testing technology, RD1-TT test a multitude of BAE Systems components, both 3D printed and composites, in the heart of the Samlesbury Enterprise Zone in Preston.
Earlier this year, UK-based engineering company Theta Technologies announced their first commercially available non-destructive testing product, RD1-TT. The machine, which has been under development for several years, utilises Theta’s unique nonlinear resonance NDT technology and has been specifically designed to provide a cost-effective, rapid flaw detection solution for metal additive manufacturers.
RD1-TT is now ready to start revolutionising metal additive manufacturing processess.
Theta Technologies believes that the machine is now ready to start revolutionising metal additive manufacturing testing processes, particularly for parts produced for critical applications in industries such as defence, aerospace, automotive and nuclear energy. The potential that the technology unlocks for additive manufacturers has peaked the interest of several major players in those key industries, with aerospace and defence manufacturer BAE Systems set to become one of the first organisations to put RD1-TT through its paces.
The collaboration between BAE Systems and Theta Technologies has been developing since the manufacturers became aware of the technological developments on nonlinear resonance testing several years ago. The company was seeking a new non-destructive testing solution that would not only allow them to simplify the overall testing process, but also significantly reduce the possibilities of working with flawed components over longer periods of time. When BAE Systems learned of Theta’s revolutionary technique, they saw potential in this providing a quick hit solution to identifying defects earlier in the manufacturing process. BAE Systems believe that nonlinear resonance is going to be key to developing quick, whole item testing that can be used to support, and confirm the in-process assessment of parts, with composites proving a key focus.
We’re impressed with Theta technologies innovative NDT methods and excited to work together to assess RD1-TT
Kevin Pickup, Lead Technologist – Product Verification, BAE Systems Air sector “As we evolve our manufacturing processes we recognise new opportunities and advances in inspection capability. New and novel methods of verifying the product has been made correctly, right first time and aiming for no fault forward are something we are always looking to explore and exploit. We are impressed by Theta Technologies innovative NDT methods and excited to work together to assess the RD1-TT, to understand how it can be effectively embedded within our production lines, and across our product range.”
The development of new technology is not without its challenges, and CEO of Theta Technologies, Steve Butler recognises that this is a significant step forward for the company, not only when it comes to validating the technology, but also to assist in the development of future products. “To have a major international aerospace and defence manufacturer express such an interest in our technology is a tremendous boost for us.
This collaboration will help us to gather further evidence of our technologies’ capabilities and allow us to validate what we know it can do.” Steve added, “It’s also extremely important for us to use this project to understand the challenges that manufacturers face with regards to their manufacturing and testing processes so that we can continue to develop existing and future products to maximise the benefit to our customers.”
The potential impact of Theta’s technology, in particular for the development of metal additive manufacturing, has also gained the attention of AMRC North West, part of the University of Sheffield Advanced Manufacturing Research Centre (AMRC) and the High Value Manufacturing (HVM) Catapult. This applied research centre, which sits at the heart of the Samlesbury Enterprise Zone in Preston, sees significant potential in the technology in the future development and adoption of metal additive manufacturing.
We are excited to participate in this project to test the feasibility of this new NDT technique
Dr James Hughes, research director for AMRC North West, said: “We are very excited to participate in this project to test the feasibility of this new NDT technique developed by Theta Technologies, and to assess the usability as an evaluation tool needed to address the quality control challenges encountered in AM. “As a part of the consortium, AMRC North West will work on the measurement system analysis and applicability of the technique on a wide range of products with different materials and geometries provided by BAE Systems.”
As a result of the collaboration between the three parties, an RD1-TT unit will soon be based within Additive Manufacturing Research Centre where it will be testing a variety of BAE Systems manufactured components including 3D printed metals and composites.
other publications
Whether you’re looking to stay up-to-date with our latest news or read about how our game-changing non-destructive testing technology is helping our customers, we’re certain that our rapidly expanding digital publication library has something for you.
Issue #1
Theta Technology News
BAE Systems and AMRC North West put RD1-TT to the test in major collaboration
Issue #1
The Case Study
Nonlinear resonance NDT: Unlocking the design potential of metal AM. Featuring Puntozero and m4p material solutions GMBH
learn more
Find out more about this revolutionary NDT technology from the team that built it.
Theta Technologies Limited
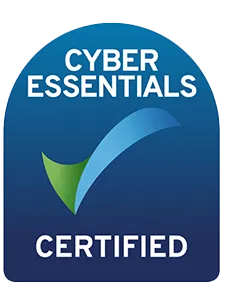
Address
Theta Technologies Limited
3 Babbage Way
Exeter Science Park
Clyst Honiton
Exeter
EX5 2FN
United Kingdom
Terms & Conditions Privacy & Cookie Policy Anti-Slavery Policy © Theta Technologies. 2024