What is Non-Destructive Testing?
Topics
What is non-destructive testing?
Industry Applications
Aerospace, Defence, Motorsport, Automotive, Oil and Gas, Medical, Power Generation, Renewables, Research Institutes.
Non-destructive testing (NDT) is an inspection and analysis technique used in manufacturing, and in-service maintenance and repair to assess a component’s integrity and suitability for use. Typically used for parts manufactured for safety-critical applications, NDT, also known as Non-Destructive Evaluation (NDE) or Non-Destructive Inspection (NDI), tests parts for potential vulnerabilities without destroying them, rendering them viable for use in their intended application.
Understanding non-destructive testing (NDT): An introductory guide
Assessing the integrity of manufactured components is not just a matter of quality, but a critical factor in ensuring safety, reliability, and performance. Manufacturers across various industries face increasing challenges to ensure that every part, whether a critical element in an aerospace structure, or in a smaller medical device, meets stringent standards. The advancement of 3D printing has complicated part inspection even further. Non-Destructive Testing (NDT) emerges as a pivotal solution in this context. But what is non-destructive testing?
As the name suggests, non-destructive testing (NDT), is a method that allows engineers to evaluate and ensure the integrity of manufactured parts without causing damage or compromising their functionality. Here we explore traditional NDT techniques, their application in additive manufacturing, and how NDT stands apart from other quality control methods, offering a comprehensive approach to maintaining the highest standards in manufacturing.
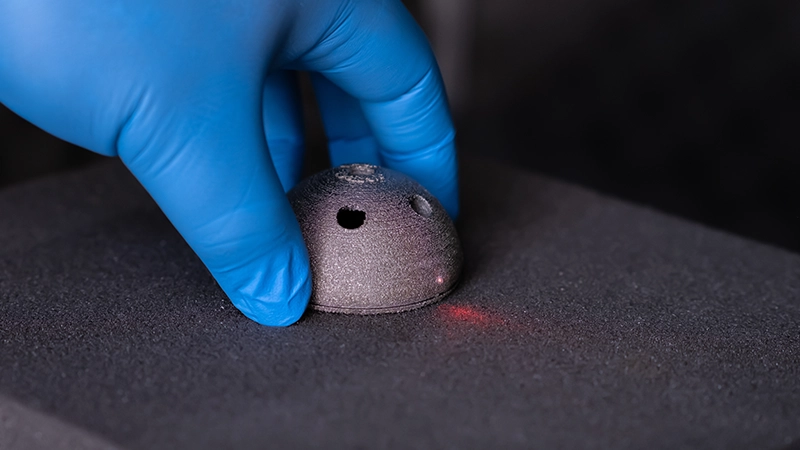
What is non-destructive testing (NDT)?
Non-Destructive Testing is a collection of analysis techniques used in science and industry to evaluate the properties of a material, or component without causing damage. Unlike destructive testing, which requires the test object to be cut, broken, or otherwise altered, NDT allows for inspection without compromising the item’s usability. This feature is crucial in industries where product integrity is non-negotiable.
Traditional NDT Techniques
NDT is an umbrella term encompassing various inspection methods, each suited to different applications and materials. Some of the more traditional NDT techniques include:
- Ultrasonic Testing (UT): Uses high-frequency sound waves to detect internal flaws or characterise materials.
- Radiographic Testing (RT): Employs X-rays or gamma rays to view the internal structure of a component.
- Magnetic Particle Testing (MT): Detects surface and near-surface discontinuities in ferromagnetic materials.
- Dye Penetrant Testing (PT): Reveals surface-breaking defects in non-porous materials.
- Visual Testing (VT): The most basic form of NDT, involving direct visual inspection or the use of optical tools.
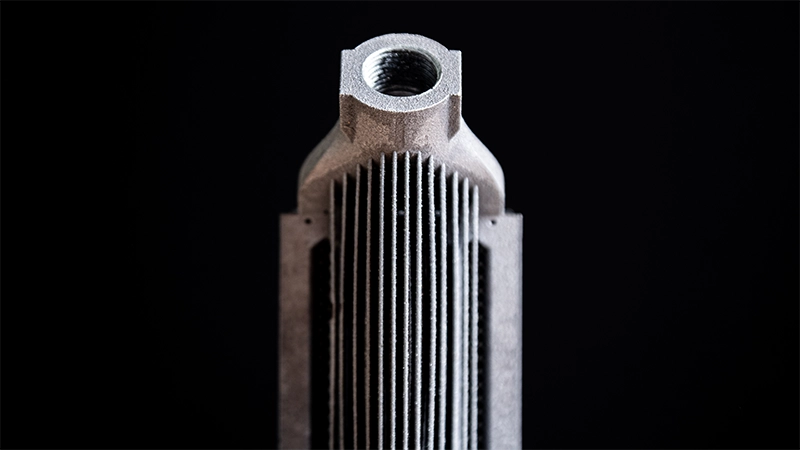
Inspection Challenges in Additive Manufacturing
Additive manufacturing, or 3D printing, has revolutionised how we manufacture and offers the unparalleled ability to create complex components. However, the layered nature of these manufacturing processes introduces unique challenges when it comes to quality control.
NDT plays a vital role in ensuring the integrity of 3D-printed parts. However, the more traditional inspection techniques have underperformed in this area. This has held back the widespread adoption of additive manufacturing. In reality, the only effective solution for the detection of internal defects that could compromise the strength and functionality of printed objects is Theta Technologies’ very own Nonlinear Resonance technique.
How does NDT differ from other Quality Control and Inspection Measures?
While traditional quality control methods often rely on sampling and destructive testing, NDT provides a comprehensive and non-invasive approach. It allows for the inspection of each component or a larger percentage of parts in a production lot, leading to higher assurance of quality and safety. Moreover, NDT’s ability to detect both surface and subsurface defects early in the manufacturing process reduces the risk of failures and enhances the reliability of the final product.
Destructive vs Non-destructive testing
Destructive testing, as the name implies, involves methods that permanently alter or destroy the part being tested. This approach is often used to determine the physical properties of materials, such as tensile strength, elongation, and impact resistance, through tests that push the materials to their failure points. On the other hand, non-destructive testing is characterised by its ability to assess the integrity and properties of a component without causing any harm or reduction in its usefulness.
NDT is invaluable for ongoing monitoring, quality control, and ensuring compliance with safety standards, especially in industries where the continuous functionality and reliability of components are critical. While DT provides definitive data on material properties, NDT offers the advantage of inspecting parts in their operational state, allowing for early detection of flaws and preventing potential failures without the need to sacrifice any parts for testing purposes.
Purpose
Non-destructive testing
Evaluates the properties and integrity of a material or component without causing damage.
Destructive testing
Assesses material properties and performance by testing to failure, or permanently altering, the material.
Impact on tested samples
Non-destructive testing
Leaves the sample intact and unaltered, allowing it to be used in actual applications.
Destructive testing
Destroys or alters the sample, rendering it unusable for its intended purpose.
Application
Non-destructive testing
Ideal for ongoing monitoring, quality control, and safety compliance in operational settings.
Destructive testing
Suitable for laboratory testing, material research, and determining physical properties of materials.
Cost-effectiveness
Non-destructive testing
More cost-effective for large-scale or continuous testing as it does not destroy the parts being tested.
Destructive testing
Can be more expensive in the long run due to the need for multiple samples and the destruction of tested parts.
Data and results
Non-destructive testing
Provides indirect measurements and indications of flaws or inconsistencies, often requiring expert interpretation.
Destructive testing
Offers direct, quantitative data about material properties like tensile strength, elongation, and hardness.
Industry Preference
Non-destructive testing
Preferred in industries where safety and reliability are critical, such as aerospace, automotive, and power generation.
Destructive testing
Often more time consuming due to the need for sample preparation and the testing process itself.
Time Efficiency
Non-destructive testing
Generally quicker as it does not require the destruction of the part, allowing for faster inspection cycles.
Destructive testing
Destroys or alters the sample, rendering it unusable for its intended purpose.
Sample Size
Non-destructive testing
With techniques such as nonlinear resonance, can inspect 100% of a production lot without issue.
Destructive testing
Typically requires a smaller, representative sample from a batch due to the destructive nature of the tests.
NDT: The right option for you?
Non-Destructive Testing is an indispensable tool in the engineer’s arsenal, offering a blend of safety, efficiency, and thoroughness that is unmatched by traditional quality control methods. As manufacturing technologies evolve, especially with the rise of additive manufacturing, the role of NDT is set to become even more pivotal in ensuring that the innovations of today meet the stringent safety, quality and part performance demands.
Contact the Theta Technologies team…
Tell us how we can help you unlock additive manufacturing potential.
Theta Technologies Limited
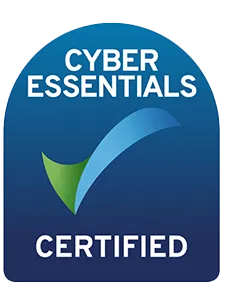
Address
Theta Technologies Limited
3 Babbage Way
Exeter Science Park
Clyst Honiton
Exeter
EX5 2FN
United Kingdom
Terms & Conditions Privacy & Cookie Policy Anti-Slavery Policy © Theta Technologies. 2024