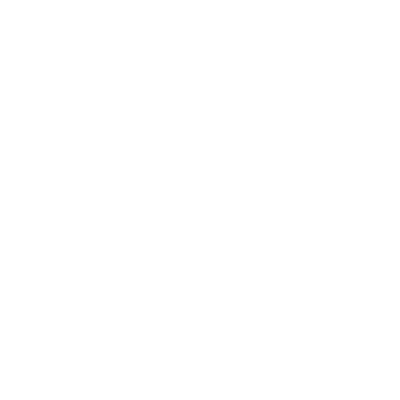
inside AM
A P O D C A S T B Y T H E T A T E C H N O L O G I E S
Episode 3:
Advancing Additive Manufacturing: Insights from Enrico Gallino on Innovations, Challenges, and Future Directions
Episode 3 of “Inside AM,” the podcast series by Theta Technologies is here! In this episode, we sit down with Senior Engineer at Ricoh 3D, Enrico Gallino to explore the cutting-edge advancements in additive manufacturing. We delve into the transformative potential of composite materials and discuss the key comparisons between tensile stress testing and nonlinear resonance NDT for quality assurance of AM parts. Enrico also shares his insights on how collaboration within the AM ecosystem is key to unlocking broader adoption and innovation.
In This Episode
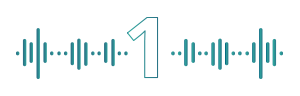
The Role of Composite Materials in 3D Printing
Enrico discusses the advantages of composite materials in additive manufacturing, emphasising their lightweight properties and potential to replace metals in high-performance applications.
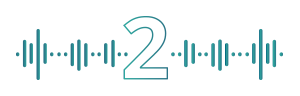
Tensile Testing vs
Nonlinear Resonance NDT
Explore the innovative comparison between traditional tensile stress testing and nonlinear resonance non-destructive testing (NDT), highlighting their complementary roles in ensuring the quality and reliability of 3D-printed components.
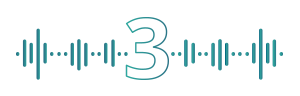
Collaborative Innovation in Additive Manufacturing
Enrico highlights the importance of collaboration across the additive manufacturing ecosystem, advocating for partnerships, education, and the integration of new technologies to drive wider adoption and unlock the full potential of AM.
Advancing Additive Manufacturing: Insights from Enrico Gallino on Innovations, Challenges, and Future Directions
In our latest episode of the insideAM podcast, we were thrilled to welcome Enrico Gallino, a name synonymous with the additive manufacturing (AM) industry. Joining host, Chris Parker, Senior Engineer of Additive Manufacturing at Ricoh 3D, Enrico delves into the transformative potential and current challenges of AM.
The range of topics covered in our most recent discussion is vast, with a special focus on composite materials, and a follow-up on a collaborative study between Theta Technologies and Ricoh 3D designed to assess the potential of nonlinear resonance NDT to replace increasingly outdated tensile stress testing part inspection methods for additive manufactured parts.
Optimising Design for Additive Manufacturing
One of the pivotal points Enrico emphasised throughout his discussion was the necessity of understanding the specific application to optimise component design. Techniques such as topology optimisation and generative design are crucial in this process. These methods help tailor the component design to meet the exact needs of the application, enhancing performance and efficiency.
Enrico highlighted examples from a recent ‘Beyond Print’ event, where several companies showcased solutions aimed at optimising component design for AM. These solutions underscore the importance of not merely choosing AM for its novelty but ensuring that the parts are designed specifically to exploit the versatility and strengths of the technology.
Challenges in Additive Manufacturing Implementation
Despite its promise, the implementation of AM is not without challenges. Enrico shared experiences where companies adopted AM because it seemed the right move, only to find that their parts were not well-suited to the technology. For instance, while AM can be excellent for prototyping, scaling up to production might require a different approach if the parts are not optimised for AM.
Enrico stressed the importance of dialogue with customers to share best practices and provide consultancy. This approach ensures that parts are not just printed but are optimised for the AM process, making the most of the technology’s capabilities.
The Role of Materials in Additive Manufacturing
The range of materials available for 3D printing plays a significant role in its application. Polymers have led the way in 3D printing, with Ricoh 3D focusing on this material since 2019. Polypropylene, in particular, has been a unique offering from Ricoh 3D. In recent years, strategic partnerships have expanded the material portfolio to include composites. Enrico mentioned a notable collaboration with Impossible Objects, which has brought new composite materials into the mix.
Composite Materials: The Future of 3D Printing
Composite materials have shown immense potential due to their lightweight properties and ability to replace metals in specific applications. Enrico discussed the benefits of composites, particularly in sectors like aerospace and automotive, where reducing weight is crucial. The ability to print high-performance materials like PEEK, known for its chemical and thermal resistance, opens up new applications.
Enrico explained the advantages of composite-based additive manufacturing (CBAM) technology, a relatively new approach that offers significant benefits in strength, speed, and cost. CBAM technology is notably faster than other composite technologies and is designed for serial production, making it suitable for a wide range of applications, from aerospace components to consumer goods.
Metal Additive Manufacturing: Overcoming Barriers
While polymers have seen widespread adoption, metals have been slower to gain traction. Enrico attributed this to the challenges associated with high-value applications that require stringent qualification processes. However, metals are increasingly being used in aerospace, medical, and defence sectors. As costs decrease and technologies improve, metal AM is expected to see broader adoption.
Ensuring Quality: Comparing Tensile Testing and Nonlinear Resonance NDT
Quality control is paramount in additive manufacturing, especially for high-value applications. Traditional methods like tensile testing provide valuable data but have limitations. Enrico discussed the benefits of nonlinear resonance technology as a complementary method to tensile testing.
Nonlinear resonance NDT allows for non-destructive testing of components, offering quick validation without destroying the part. This is particularly beneficial for complex geometries that are difficult to inspect using conventional methods. Enrico highlighted a case study involving a collaboration with Theta Technologies, where they explored the correlation between tensile stress testing and nonlinear resonance NDT.
In the podcast, Enrico detailed a recent collaboration with Data that showcased the potential of combining tensile testing with nonlinear resonance NDT. The case study involved testing dog bone samples to establish a correlation between tensile strength and damage index. The findings demonstrated that this combined approach could effectively identify defects and ensure the quality of 3D-printed components.
Enrico explained that the goal was to demonstrate that nonlinear resonance technology could work on parts made with specific AM processes. They tested tensile rods and found a correlation between tensile strength and damage index, even creating artificial defects to further validate the technology. The results showed that nonlinear resonance NDT could quickly and accurately identify defects, providing a valuable complement to traditional tensile testing.
The Importance of Validation and Inspection
Enrico underscored the importance of validation and inspection in ensuring the quality of AM components. Traditional methods like tensile testing still have their place, but complementary methods like nonlinear resonance NDT offer significant advantages. By providing quick, non-destructive testing, these methods can help identify defects early in the process, saving time and resources. This approach is particularly valuable for high-value applications where quality is critical. By using a combination of traditional and innovative testing methods, manufacturers can ensure the reliability and performance of their AM components.
insideAM Episode 3 featuring Enrico Galino is available now!
In summary, the conversation with Enrico Galino highlighted the transformative potential of additive manufacturing, the importance of quality control, and the need for collaboration and education within the industry. By addressing these key areas, the industry can unlock new applications and drive wider adoption of this revolutionary technology.
Watch the full episode now.
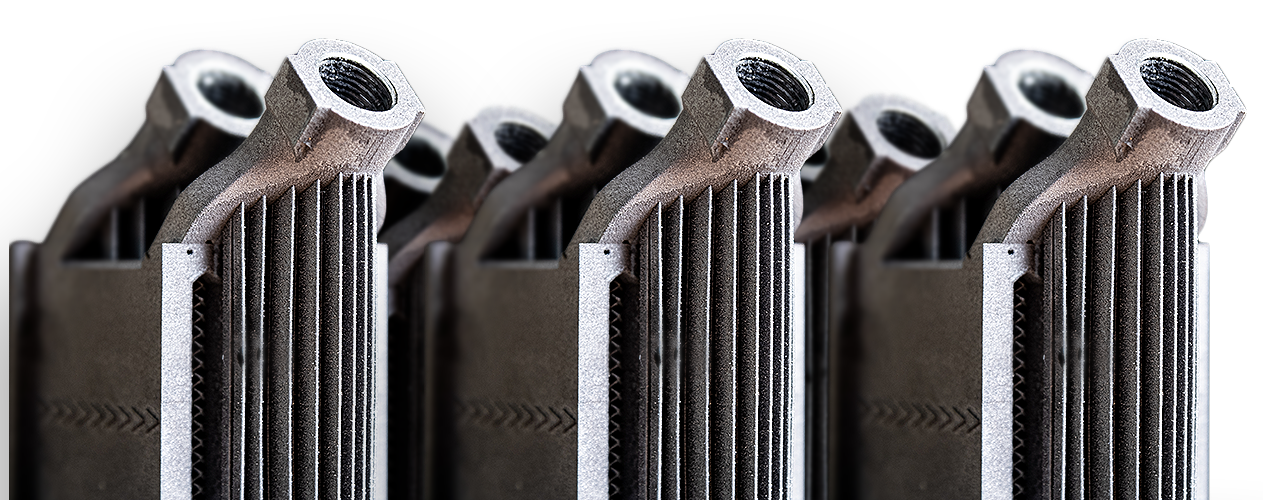
BOOK A FREE
NON-DESTRUCTIVE PART TEST
Discover how effective our nonlinear resonance NDT solution is with a complementary part test.
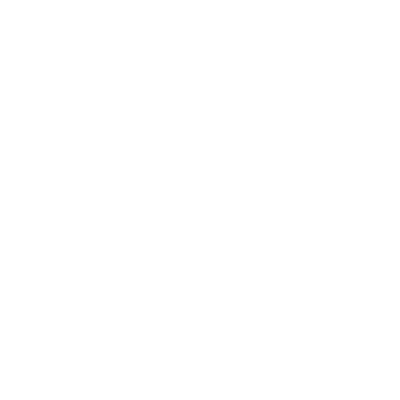
Talk to
Our Team of
Technical Specialists
Connect with our team of technical experts today and explore how RD1-TT can help revolutionise your additive manufacturing processes.
Theta Technologies Limited
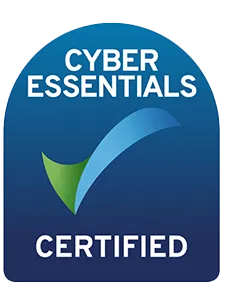
Address
Theta Technologies Limited
3 Babbage Way
Exeter Science Park
Clyst Honiton
Exeter
EX5 2FN
United Kingdom
Terms & Conditions Privacy & Cookie Policy Anti-Slavery Policy © Theta Technologies. 2024