NDT for AM
Medical Device Inspection
With patient safety of paramount importance, ensuring the integrity of complex AM medical devices is key. With traditional inspection methods falling short, this remains a significant industry challenge. Our very own Technology Manager, Daniel Sanmartin, explains how nonlinear resonance NDT is the ideal solution for the part qualification of AM medical devices.
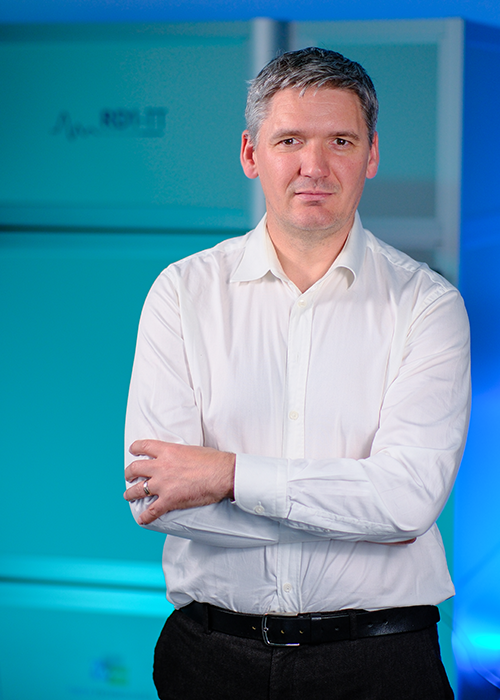
Daniel Sanmartin
Technology Manager, Theta Technologies
Daniel has over 15 years of experience working on Science and Engineering projects funded by both industry and academic institutions. Originally from Spain, where he obtained his first degree in Physics, he went on to obtain a Ph.D. at the University of Birmingham on Piezoelectric devices in 2011. Daniel joined Theta Technologies in 2017 and is responsible for driving the research and development activities necessary to develop existing products so they can meet the application requirements of Theta’s customers.
“We are not relying on tensile specimens or test structures produced alongside the build”
In Context: AM Medical Device Inspection
With additive manufacturing (AM) rapidly gaining traction in the medical sector, creating new and improved opportunities for customised implants and prosthetics. But with patient safety the number one concern, the stakes couldn’t be higher in ensuring the integrity of these complex AM parts. This remains a significant challenge in the medical sector, especially when traditional non-destructive testing (NDT) methods fall short.
Fortunately, we have an expert on hand to help you navigate this challenging landscape. Daniel Sanmartin, Technology Manager at Theta Technologies, discusses the transformative potential of nonlinear resonance NDT for medical device manufacturers. With insights on how this innovative technology offers a more reliable, efficient, and scalable approach to AM part qualification.
The interview covers how nonlinear resonance NDT allows manufacturers to test the actual medical devices themselves, without the need for additional test structures or tensile specimens, making it particularly valuable for complex AM parts. The technology not only enhances part qualification but also addresses the specific challenges of the medical industry, such as minimising patient risk, reducing manufacturing costs, and improving production efficiency.
Read on to explore how Theta Technologies’ nonlinear resonance NDT is reshaping part inspection processes for medical AM devices, and why this technology is a must for manufacturers looking to ensure the highest safety standards.
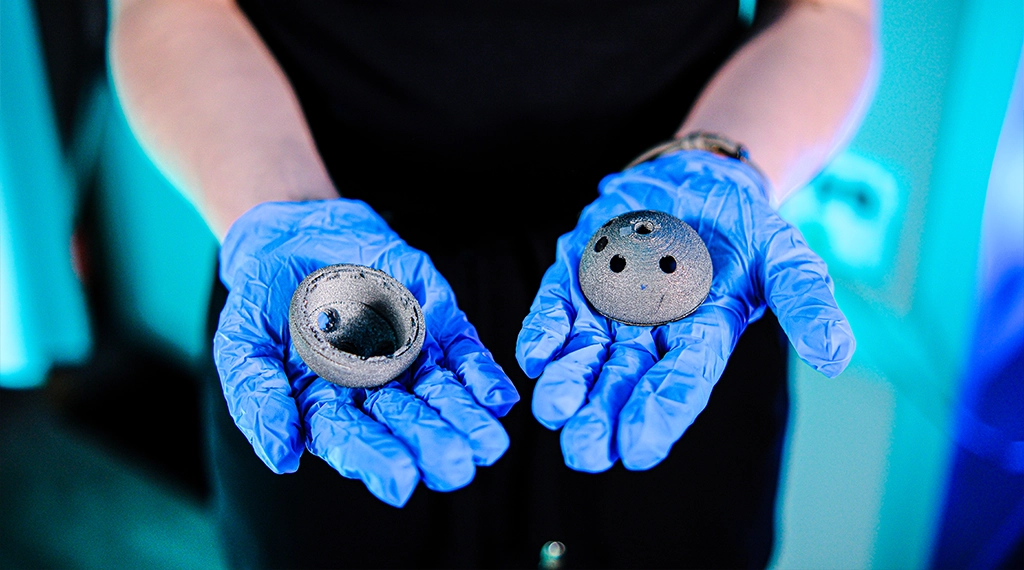
The Interview
So, we’re focusing specifically on the medical industry here. There’s been an increased adoption of additive manufacturing within that space. But let’s start at the very beginning in terms of parts that are destined to be implanted into individuals. Why is part inspection so important for that?
Part inspection is crucial for the medical sector because the cost of failure on a part implanted in the human body is very high. From the manufacturer’s perspective it is something that is to be avoided at all costs because it will bring reputational and litigation costs that they will want to try to avoid. Therefore, ensuring that parts are of the highest quality and risk of failure is as low as possible, once they are deployed and used in theatre is of the highest possible priority for all the stakeholders in the medical industry.
And what are the consequences of parts failing?
The ultimate consequence of parts failing is a patient needing to have the parts to be removed and the complications that come with that. So, the specific operations that need to happen as a result of part failure. Then from the vendors or manufacturer perspective, the litigation costs that may come from parts failing while in use. Those can be very high as well.
What are the current part inspection methods the manufacturers for medical scenarios using to actually inspect the integrity of these parts before they are implanted?
So, there are different methods used. First, is to prove the quality of the materials being employed and used. This is [typically] done based on tensile specimens. Tensile specimen standards date back several decades because they are used for traditional manufacturing methods. But everybody knows that they are not representative of a part quality for additive manufacturing components. That’s one way of qualifying your materials in terms of the AM parts themselves.
X-Ray radiography is something they use during the development of the parts which can help new processes as they are implemented, and to identify the flaws within those components. Then optical inspection methods where essentially you have inspectors looking at components under a high magnification, optical microscope and looking for surface breaking flaws on the parts. Those are the alternative methods that they are mostly being used now.
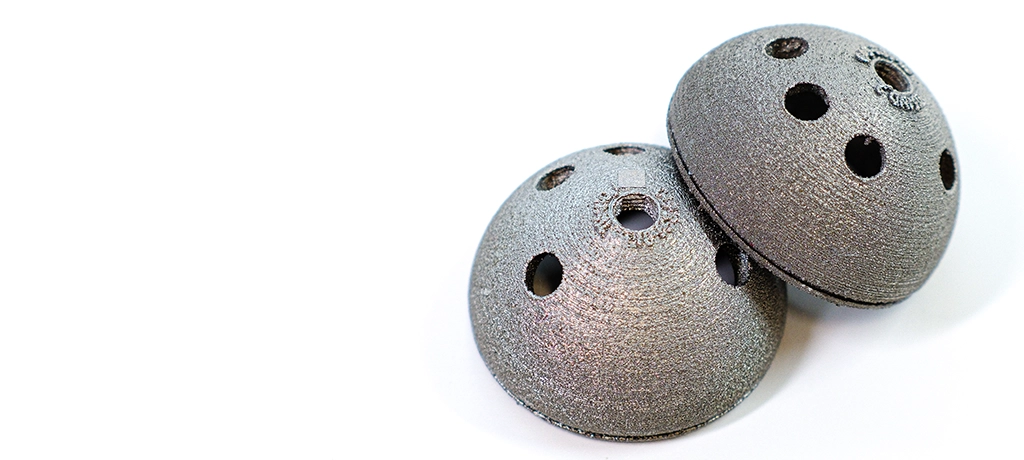
“This innovation has the benefit of freeing up space on your build which allows you to produce a larger number of parts”
So where can nonlinear resonance help the medical sector in particular when it comes to their part inspection?
The main way that nonlinear resonance can help is that resonance responses can be obtained from the medical devices themselves rather than relying on tensile specimens. So, you can obtain information about your materials, your processes and how uniform they are using our method. This is information that you can obtain based on the medical devices themselves. Also, you can use our technique to check whether you have a critical flaw on the structure. Things like cracks or lack of fusion flaws and the way that these behave. These make your processes uncontrolled and that’s something that we can pick up using our nonlinear resonance technique.
In terms of failure, certainly within medical, where can those parts actually begin to fail? Can they fail from the very start right up until the point of actually being implanted into people? Where are these part failures likely to happen and can nonlinear resonance help identify that throughout the process?
The first point of failure is on the part after a build. There could be stress features that could be unintentionally added to those parts. These stress-adding features, could result in things like cracks developing on parts. That’s the first stage where flaws can happen. Then during the heat treatment process, parts can be stressed, and flaws can happen at that stage as well. These stress-raising features can lead to cracks propagating on the structure. Finally, after machining the part when the support structures are removed. The part is machined into the final product and some of those processes are still quite manual and there is a high opportunity for things not to go according to plan.
What’s your final message to medical companies, whether that be the manufacturers or the actual end user. What would be your message about why nonlinear resonance should be on their radar?
Nonlinear measurements can be obtained from the AM devices themselves. So that’s the first one that’s very important because it means that we are not relying on tensile specimens or test structures built alongside the build. We know that they are not representative of part quality. Our innovation has the benefit of freeing up space on your build which allows you to produce a larger number of parts that otherwise would have been impossible.
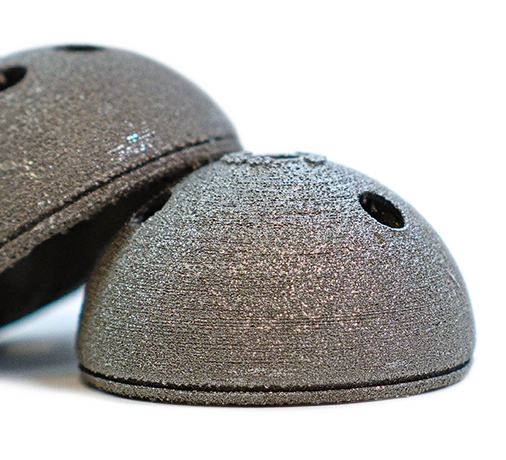
Book Your
Complimentary
Technology Demonstration
Discover how nonlinear resonance NDT can help you deliver robust, high-performance AM medical devices with a personalised demonstration.
NDT Resources and Articles
Featured Article
The benefits of using nonlinear resonance NDT for the part qualification of AM medical devices
Additive manufacturing (AM) offers unprecedented opportunities for creating customised medical devices, implants, and prosthetics. However, with this innovation comes the critical challenge of ensuring that these devices meet the strict safety and reliability standards required for medical applications. Explore the future of AM medical device part qualification.
Recent Articles
Resources to help you navigate the world of NDT for additive manufacturing.
We understand the part qualification challenges faced by those embracing additive manufacturing. That’s why we’re committed to providing you with valuable and insightful content to help navigate this increasingly complex landscape.
Explore our latest articles on a range of key industry topics:
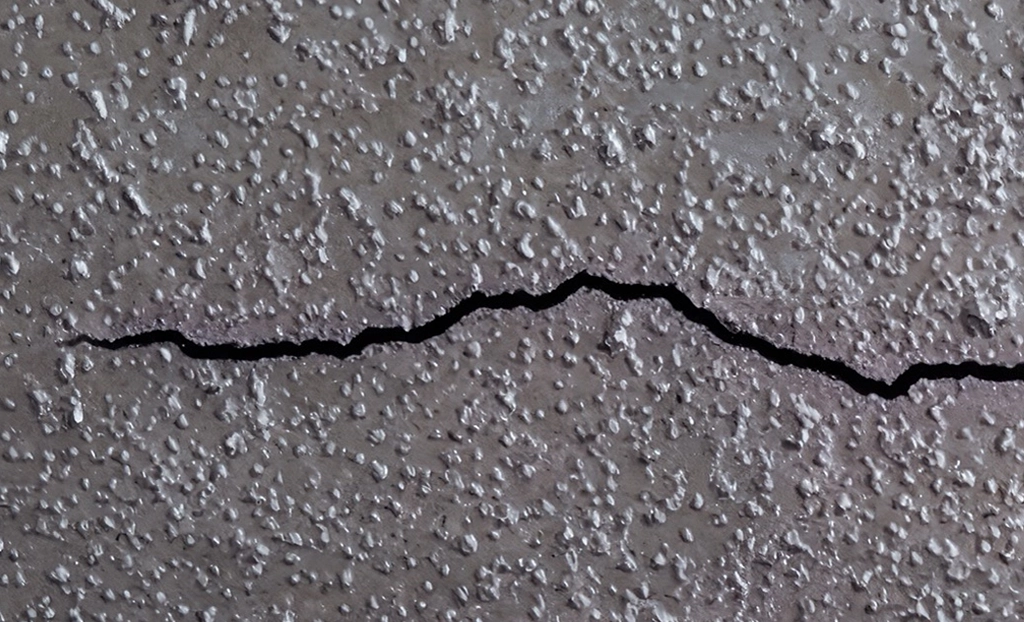
Topic: AM Flaw Detection
AM flaw types, the consequences of leaving undetected, and the NDT solution you need
Learn about the common flaw types found within additive manufactured components and discover how nonlinear resonance NDT can help identify them before they become an issue.
READ NOW
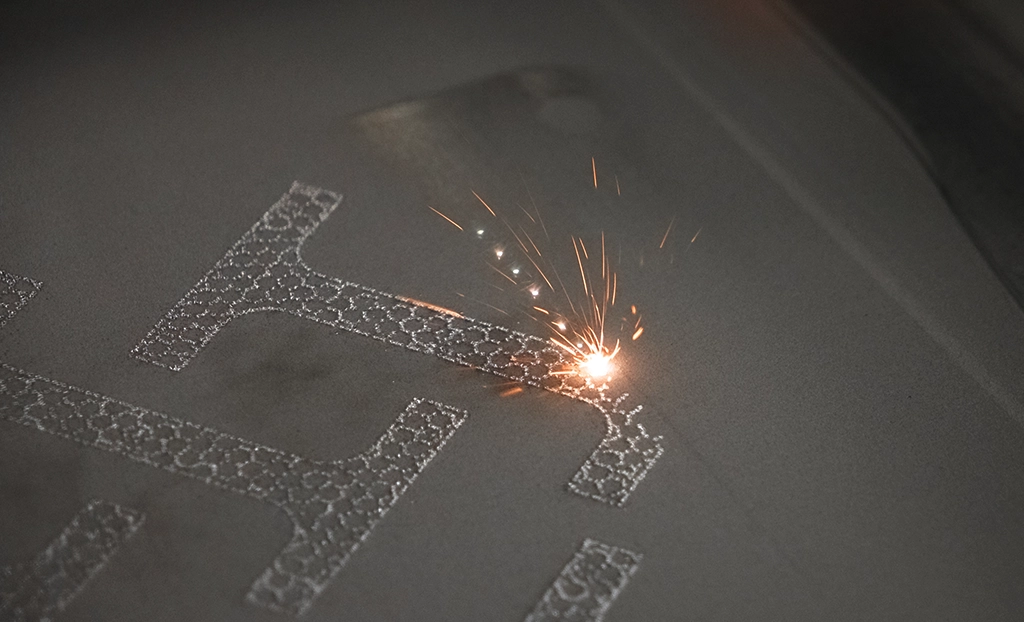
Topic: Additive Manufacturing
How to solve additive manufacturing part qualification challenges with effective NDT
Addressing the unique part inspection challenges of additive manufacturing is continuing to be one of the biggest obstacles preventing its wider adoption. Learn how to solve these challenges.
READ NOW
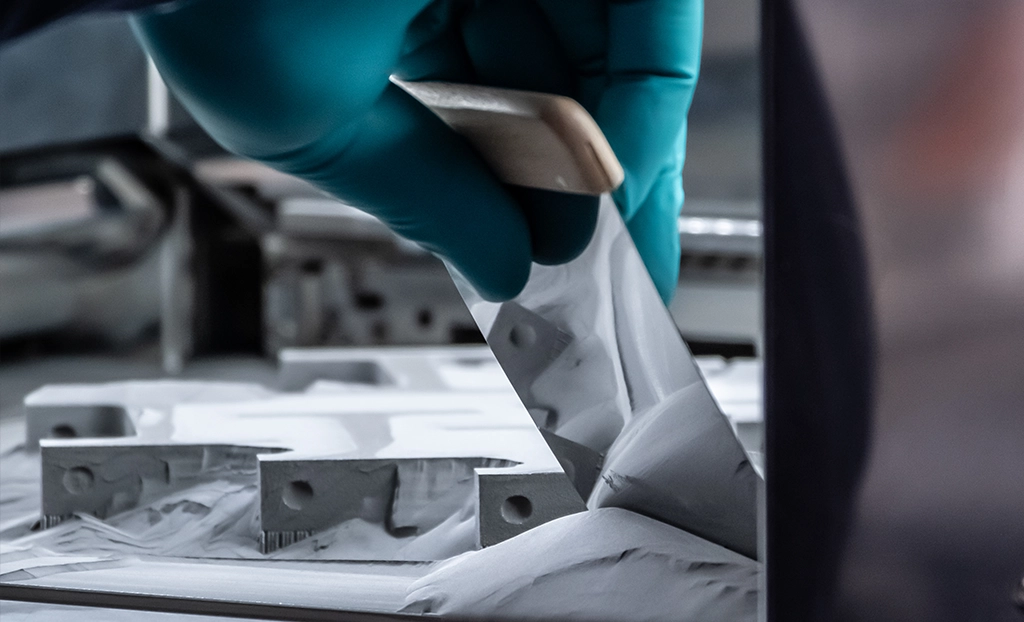
Topic: AM Post-Processing
Reducing the risk of adding value to AM parts at post-processing with immediate inspection
Deploying effective NDT earlier in your manufacturing process is key to reducing unnecessary value being added to defective parts during post-processing. Find out how nonlinear resonance can help.
READ NOW
Theta Technologies Limited
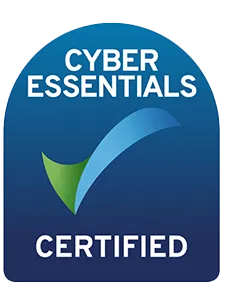
Address
Theta Technologies Limited
3 Babbage Way
Exeter Science Park
Clyst Honiton
Exeter
EX5 2FN
United Kingdom
Terms & Conditions Privacy & Cookie Policy Anti-Slavery Policy © Theta Technologies. 2024